Diecasting is an extremely specialized manufacturing process that transforms hot metal into precisely-defined components using high-pressure molds. This technique has become indispensable for a wide range of industries such as automotive, aerospace, electronics and even consumer products because it can create complex forms with incredible precision and consistency. In combining the principles of metalworking with the latest in engineering it provides unparalleled precision and efficiency, making it a fundamental element of contemporary manufacturing. This article explores the complicated world of diecasting, studying its processes, benefits, and wide-ranging applications.

Diecasting is the usage of molds, also known as dies. Dies are created out of high-quality stainless steel, which can stand the harsh conditions that are encountered during the casting process. Die designs are made using precision and often incorporate elaborate details and precise tolerances that ensure the final product's accuracy. The process of diecasting involves molten metal-commonly aluminum, zinc, magnesium, or copper-is injected into the dies at high pressures. This quick injection and subsequent solidification result in components with exceptional dimensional stability, as well as a perfect surface finish that reduces the need for further manufacturing or finishing. The preciseness of the dies permits the creation of geometries with complex shapes that might be impossible or difficult for other production methods.
One of the primary advantages of diecasting is the capacity to make parts with outstanding dimensional precision and smooth surface finishes. High-pressure injection guarantees that every detail of the mold is replicated making parts with tight tolerances, and require minimal to none post-production tasks. This precision is particularly advantageous to create complex geometries and intricate details that are difficult or impossible to achieve by other techniques of manufacture. Also, the repeatability of diecasting is ideal to produce large quantities, and ensures uniformity across a large number of parts. The efficiency of the process also leads to significant cost savings since it can reduce material waste as well as labor expenses.
Diecasting is also a great option in terms of mechanical properties. Components produced through diecasting typically exhibit excellent strength and durability due to the fine-grain structure created during the fast cooling of the molten metal. This makes diecast parts suitable for any applications that require top performance and dependability. Additionally, it allows for the incorporation of thin walls and intricate features, with no compromise to structural strength. This is especially beneficial in the automotive and aerospace industries, where cutting down on weight but maintaining strength is essential. The ability to produce light, but strong parts can improve the efficiency of fuel and efficiency in aircrafts and vehicles. To acquire further information please go to my blog
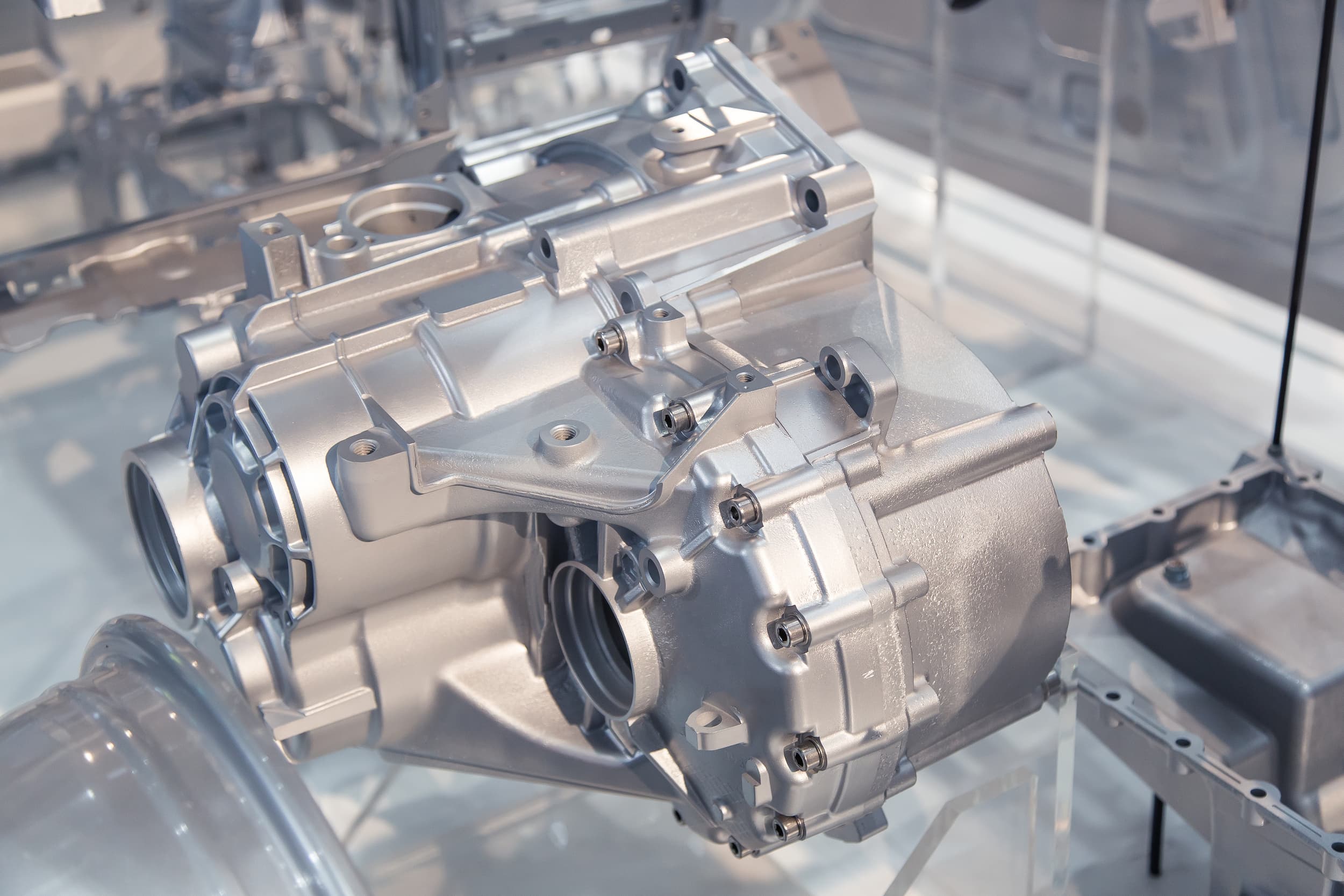
Diecasting's versatility extends to its many uses. In the auto industry, diecast components are used in transmissions, engines, and structural elements, which can contribute to more efficient and lighter automobiles. In the electronics industry, diecasting is used to create heat sinks, housings, and connectors to ensure optimal thermal management and durability. Household appliances, power tools and toys also benefit in diecasting's accuracy and efficacy in the production of components that range in size from knobs, handles, and handles and internal components. The ability of the process to work with different metals and its ability to make parts with complex designs make it suitable for many industries, each benefiting from the unique advantages of diecasting.
Diecasting is an important manufacturing process that brings together high-quality, efficient and flexibility. Its capability to make intricate, high-quality products with exceptional mechanical properties makes it indispensable in many industries. Diecasting's effectiveness when it comes to mass production, with the material and cost advantages, proves its worth for modern manufacturing. Since the need for high-quality and dependable components continues expand, diecasting is an essential technology that drives innovation and enabling the production of advanced products that meet requirements of the marketplace. Through its continued expansion and development it is a perfect example of the interaction between engineering and manufacturing proficiency, cementing its role in the future of industrial production.